It’s challenging enough to create innovative products and services that will put your business on the map.
But to then devise a process that will replicate quality every time, without fail, is another story entirely.
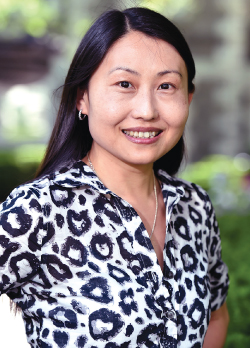
Photo by Dana Maxson
That is where Dongli Zhang, Ph.D. wields her expertise. Zhang, an assistant professor of management systems at the Gabelli School of Business, studies quality management practices—procedures that ensure a company’s products or services are of the highest caliber. In her latest paper, “Customizing Quality Management Practices: A Conceptual and Measurement Framework,” published in Decision Sciences, Zhang suggests how companies can tailor these practices to their needs.
“For the past few years, we’ve been talking about the customization of these so-called best practices—but how does a company customize them?” she said.
The key, she said, is to refine the process that generates the product or service (an activity known as process management) while accounting for environmental and organizational factors that affect companies. Process management can go one of two ways, Zhang explains in an earlier paper, “The Moderating Role of Contextual Factors on Quality Management Practices,” published in the Journal of Operations Management. A company can either seek to improve the efficiency of a process by monitoring it and working to reduce errors, or the company can take what Zhang calls an explorative approach, which means overhauling the entire process.
“If we can do good quality control on these processes as a whole—not just inspecting the finished products—then we can make sure our products will be good,” she said.
Zhang has found, however, that more goes into process management and quality control than merely creating an effective procedure for companies to follow. Cultural differences among companies can have a significant impact on operations, and, in turn, on the products and services as well.
“If you want to operate in China, you need to know the culture of Chinese operations. Likewise, if you want to operate in the U.S., you need to know the local culture here,” she said.
Unfortunately, this cultural proficiency is lacking in many businesses, she said—but not because they are unfamiliar with Chinese culture. Rather, they are not au courant with cultural shifts in the East.
In “Achieving Successful Business in China: Assessing the Changing Chinese Culture,” a paper which is forthcoming in The Journal of Asia-Pacific Business, Zhang targets assumptions that the business world tends to make about Chinese culture and how these misunderstandings influence Eastern business practices.
“We used to think that traditional Chinese culture leads businesses to be more conservative and to avoid risk,” Zhang said. “We actually found that Chinese culture is changing.”
According to her data, Eastern and Western business practices resemble one another more closely than entrepreneurs realize. Between Chinese companies increasing business relations with foreign partners, and Western companies basing their suppliers in China or even moving to China, Eastern companies have gained more exposure to Western culture in recent years.
When it comes to quality control, this culture shift has important upshots.
“If Chinese culture was still very traditional, then we would focus on certain types of practices [to control quality]. But because we have a changing culture, the practices we use will be different,” she said.
In addition to researching the relationship between culture and quality management, Zhang studies how the presence or absence of trust influences organizational structure and strategy. The extent to which trust exists throughout the supply chain—for instance, trust between manufacturer and supplier, and between manufacturer and customer—will have an impact on a business’s effectiveness, Zhang said.
“When we research the supply chain, we look at many things that can influence its effectiveness,” she said. “Some of these factors might be technical—for instance, how good the communication is along the chain. Other factors include this ‘soft’ aspect, like trust or cultural differences among the supply chain partners.
“That is something that is often misunderstood, especially as the global supply chain becomes more complex and extended. That soft aspect becomes more important for us to understand.”
For all realms of the business world, Zhang recommends a “process view.” Every task is born of some process, she says, whether one realizes it or not. With this in mind, it is important to take a step back and identify what that process entails. That way, each and every part of the process can be identified, examined, and ultimately improved.
This philosophy of “continuous improvement,” as she calls it, also makes its way into her classroom. She impresses upon her students that surviving and thriving in a society of rapid-fire developments requires individuals and communities to always seek to improve.
“That’s something I tell them—continuous improvement,” she said. “Don’t fall into thinking you are doing good enough. There is always room to improve.”